A dovetail jig and a router make building drawers with half-blind dovetail joints a sure thing — assuming everything works the way it’s supposed to. However, in the real world a dovetail jig can prove to be a bit finicky. And this sometimes makes routing dovetails an exercise in frustration.
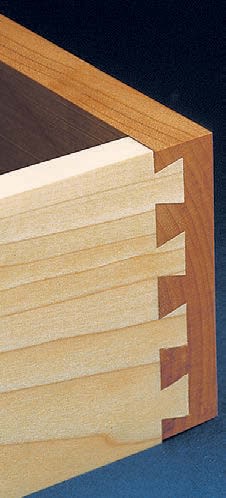
But like every woodworking operation, ensuring success is simply a matter of knowing what can go wrong and how to avoid or fix the problem. Every dovetail jig is a little bit different, but there are some universal tips, tricks, and guidelines that guarantee you’ll get the perfect-fitting dovetail joints you’re after.
SIZING & SPACING. When planning your project, it’s important to think ahead and size the height of the drawer openings and drawers to match the template spacing of your jig. The two most common spacings are on 7⁄8" and 1" centers. The goal is to end up with a half pin (or close to it) at the top and the bottom (margin photo). For example, if your jig uses a 1" spacing, the height of the drawers should be in even increments of 1".
ACCURATE PARTS. You won’t get nice-fitting joints or drawers if you start with inaccurate or inconsistent parts. So always make sure your workpieces are flat, square, and uniformly sized.
EASY ACCESS. I like to position the jig at a comfortable working height and make sure it’s clamped down tightly (photo below). You’ll also find it’s advantageous to work at a height that gives you a clear view of the cut. Finally, eliminate any clutter in the work area that might snag the router’s power cord.
A CENTERED BUSHING.
The jig’s template and the bushing in the router base work together to guide the router and bit. If the bit isn’t perfectly centered in the bushing, the cuts may not be consistent. So it’s a good idea to center the bit before getting started.
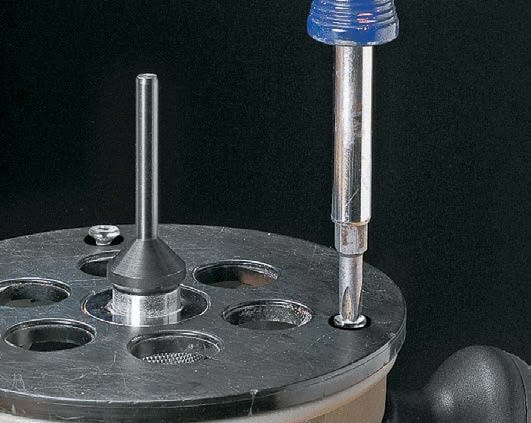
Actually, since the bit is fixed in the collet, what you’re doing is centering the bushing around the bit. This can be done easily with an inexpensive centering cone as shown in the photo above.
SECURELY CLAMPED.
You never want the workpieces to shift while you’re routing the joint. So it pays to make sure they’re held firmly beneath the clamping bars. If your jig doesn’t have grip tape on the clamping bars, consider adding some adhesivebacked sandpaper to create a non-skid surface. And when clamping narrow parts, I place a spacer under the clamping bars to keep them from racking (lead photo).
BIT HEIGHT.
The fit between the pins and tails is determined by the bit height in the router. This is your main adjustment when setting up to cut the dovetails. So the first thing I do is adjust the bit height with test cuts using stock identical in thickness to that of the drawer parts.
If the fit of the joint is too tight, you’ll need to lower the bit. The bit will then cut narrower tails and wider sockets. Too loose, and you should raise the bit to produce the opposite effect. I rely on a simple verse to help me remember which way to go, “Lower to loosen — heighten to tighten.”
A GOOD FIT. It’s always hard to know when the fit is just right. I shoot for a joint that can be assembled with only moderate pressure. You should be able to fit the tails halfway into the sockets by hand. Then a few light taps with a mallet should fully seat the tails.
SCORING PASS. It’s not uncommon to experience minor tearout along the inside edge of the tail piece. This can be avoided by starting with a light scoring pass across the front of the workpiece traveling from right to left (main photo, opposite page). Backrouting this shallow shoulder will eliminate the chance of tearout when making the full-depth cuts.
BACK & FORTH. When following the fingers on the subsequent pass, I work on keeping the router flat on the template. Since only half of the router’s base is supported by the template, the trick is to concentrate on keeping its weight balanced. And then once the first left-to-right pass is completed, I like to make a second right-to-left “insurance” pass to be certain that all the sockets and tails are cut to full depth.
FLUSH EDGES.
Even when the pins and tails fit well, the edges of the pieces may not align (photo above). The cause? One piece was not snug against the stop. The simple cure is to check the position of both workpieces before turning on the router. They should be tight against the stop as well as snug to one another and the template.
IN OR OUT. You can encounter a similar problem where the sides aren’t flush (proud or recessed) with the front and back. The fix here is to adjust the depth of the sockets by moving the template or stop bar forward or back.
NO CLAMPS. Since dovetails form a locking joint, relying on clamps at assembly is optional. My choice is to leave the clamps in the rack. It’s less stressful and it’s easier to square up the drawer. Just apply glue sparingly to the sides of the tails and sockets, tap the joint flush, and finally, check for square on a flat surface.
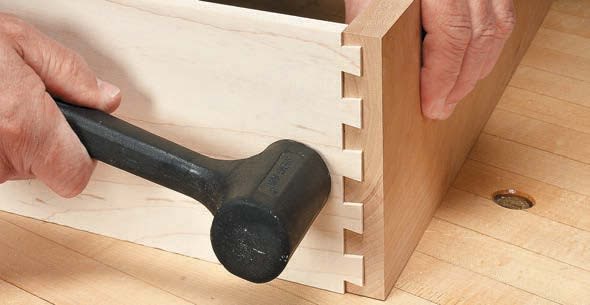