If you were to peek into most woodshops, chances are you’d find a table saw near the center of each one. With it, you can rip stock to width, crosscut workpieces to length, and create many different kinds of joinery.
It will only do these things well if you install the right blade for each task. If you don’t, you might get rough cuts, tearout, or burnt edges. Worse yet, you could risk kickback during a cut.
WHAT’S THE DIFFERENCE?
In order to learn how blades are designed for different tasks, you need to understand the common parts of the blade. You can start by taking a look at the drawing above. As you can see, the blade begins with a steel plate, and ends in teeth tipped with carbide.

Another feature of blade design is the laser cutouts in the plate. As technology improved, laser-cut expansion and anti-vibration slots were added to improve performance. These slots reduce vibration and help keep the blade cool, reducing blade warp due to heat build-up.
But it’s mainly the teeth and gullets that differentiate the three major types of blades — rip, crosscut, and combination. I’ll take a look at each of these blades individually. The type, number, and configuration of the teeth vary according to the task. The drawing below shows the shapes of the teeth and the different combinations.
RIP BLADES. Rip cuts are made along the length of a workpiece, in line with the direction of the grain. As the name implies, this cut separates the grain by ripping between the layers. For this type of cut, you don’t need a lot of teeth. In fact, too many only cause the wood to burn. A blade with 24-30 teeth and a flat-top configuration is perfect. The combination of fewer teeth and flat-top design help prevents the saw from bogging down in thick stock.
In addition to the flat-top teeth, rip blades also have deep gullets. It’s the gullets that allow the large amount of chips and dust to be carried out of the cut. If the chips can’t escape, the blade will heat up and burn the edge of the workpiece.
CROSSCUT BLADES. At the other end of the spectrum is the crosscut blade. Since a crosscut is perpendicular to the grain direction, you want more teeth to slice through the fibers rather than ripping them. The right tooth for this kind of cut has to be sharp enough to score the fibers and slice them cleanly. The alternate top bevel (ATB) teeth fill the bill perfectly. The result is a clean cut in solid wood.
You’ll find that a 60-tooth count is the norm for table saw crosscut blades. As you can see in the drawings above, the gullets of crosscut blades are shallower than the rip blades. These shallower gullets are all you need to carry away the smaller chips from a crosscut.
COMBINATION BLADE. A combination blade is a compromise between a rip and crosscut blade. It will do either task reasonably well, depending on the thickness of the stock. It also works well for plywood and other sheet goods.
You’ll normally find 40-50 teeth on a combination blade. Many combination blades add a flat-top or raker tooth to the ATB design for smoother rip cuts. This ATB-R has become common on combination blades from many manufacturers.
THIN-KERF BLADES. Another feature to consider when shopping for blades is the thickness of the blade. Crosscut, rip, and combination blades are available in both standard and thin-kerf designs. Thinkerf blades are a great choice for most saws. The plate and teeth are 25% thinner than conventional blades (usually around 3⁄32" instead of 1⁄8"). This reduces the workload for the saw and makes it easier to cut thick stock with a lower-powered saw. I keep a thin-kerf combination blade on my saw most of the time.
Finally, my best advice is to buy a top-quality product. It will pay you back every time you use your saw. No matter what the task, the right blade can improve the quality of your work.
Top-Notch Blade: Freud’s Premier Fusion
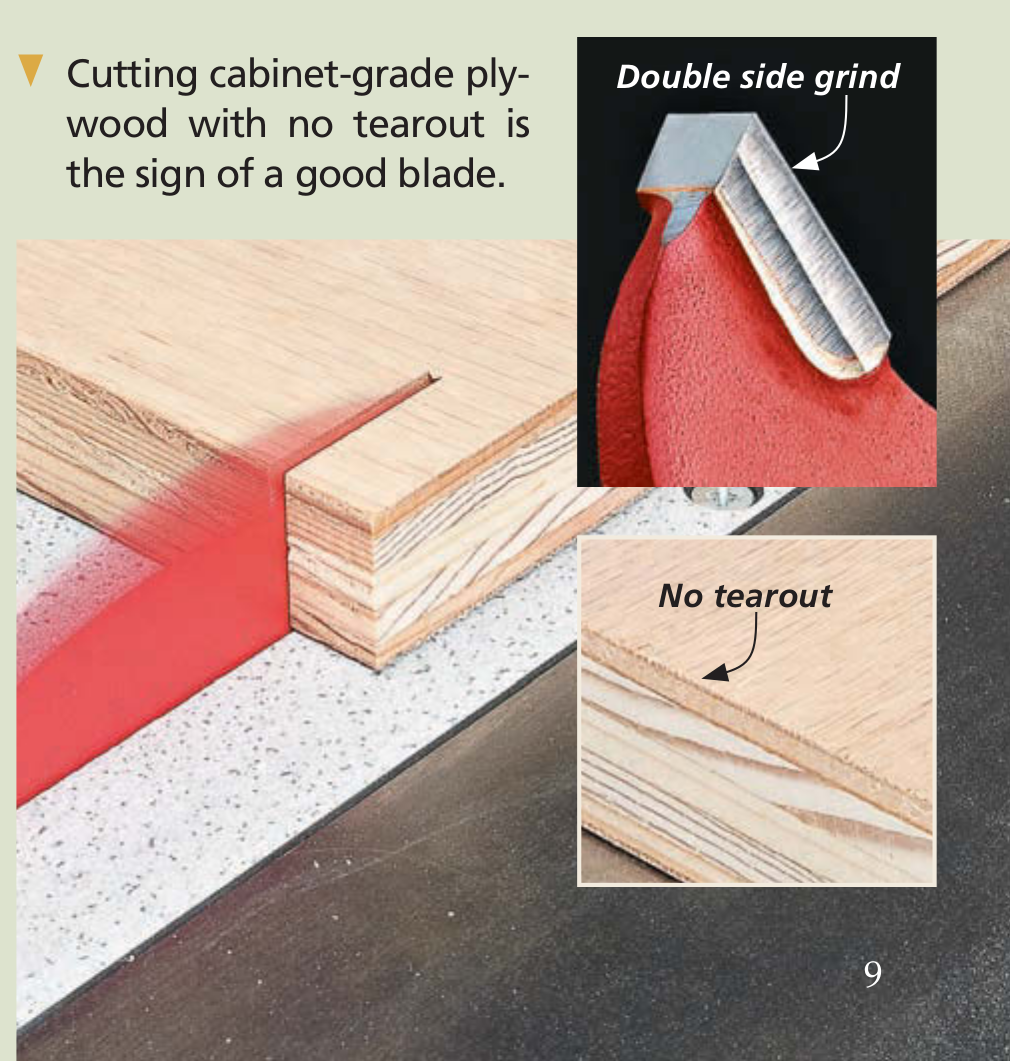
I’ve been a fan of Freud blades for many years. For me, it’s tough to beat the quality of their products for the price. Recently, I tried out their Premier Fusion combination blade. This blade is priced about 50% higher than their conventional blades, so I was anxious to see if the performance justified the cost.
WHAT IS IT? At first glance, the Premier Fusion looks like most Freud blades, right down to the familiar red, non-stick coating.
The teeth are made from Freud’s unique micro-grain carbide called TiCo — a combination of titanium and cobalt. But what’s different here is the profile of the teeth. The Hi-ATB configuration also relies on a special double side grind in the sharpening process (see inset photo at right). This creates two cutting surfaces for a smooth face on all sorts of cuts.
As you can see in the photos at right, the Fusion crosscut the face veneer of some cabinet-grade plywood without leaving a splinter. Not many blades can boast a cut that clean. Best of all, it did that and virtually every other type of cut day after day. If you really don’t like changing blades, this is the one for you.